A forrasztás egy olyan gyártási technológia, mely két (vagy több) fém alkatrész mechanikai összekötésére szolgál. A művelet során az alkatrészeket egy olvadáspontja fölé melegített majd visszahűtött forraszanyaggal szilárd kötésbe hozunk. Az elektronikai ipar elvárásának megfelelően mind a műveletben résztvevő alkatrészek, mind a forraszanyag jó villamos vezető is egyben. A forrasztásnak most kifejezetten a lágyforrasztás ágát taglaljuk, melyben a forraszanyag legtöbbször ón-ólom ötvözet, az forrasztandó alkatrész lábak pedig ónozott (vagy nyers) rézből készülnek. Fontos kiemelni, hogy a forrasztási művelet során csak az alacsonyabb olvadáspontú forraszanyag olvad meg, az összekötendő alkatrészek nem, így különösebb anyag deformáció nélkül történik a kötés, mely újra melegítéssel bontható és újra megköthető.
Forraszanyag:
A teljesség igénye nélkül csak említést teszünk rá, hogy a forraszanyag kiválasztáskor számos körülményt kellett figyelembe venni, mint például, hogy már nem sokkal az olvadáspontja felett „nedvesítse” a forrasztandó fémet, vagyis jól terüljön el a felületén; ne tartalmazzon olyan szennyező (ötvöző) elemeket, amelyek a forrasztást követően a felület korróziához vezetnek. A lágyforraszok közé tartozik az ón (Sn, olvadáspontja 231,9 °C) a bizmut (Bs, 271,3 °C), a kadmium (Cd, 320,9 °C), az ólom (Pb, 327,4 °C, 2006. július 1-jétől tilos az alkalmazása) és a cink (Zn, 419,4 °C), valamint ezek ötvözetei. A korszerű forraszanyagok az ólom (Pb) helyett rezet (Cu) tartalmaznak.
Folyasztószer:
A forraszanyag gyártmányok nagyon gyakran vékony „bél”-ként folyasztószert (pl. fenyőgyanta) is tartalmaznak, hogy a forraszanyag (használatos még a forrasztóón kifejezés is) minél könnyebben és gyorsabban terüljön el a forrasztandó felületen. A folyasztószerek többcélú kemikáliák. Feladatuk, hogy a forrasztás közvetlen környezetét megtisztítsák és a forrasztás során megvédjék a felületet a káros oxidációtól, valamint a forrasztás közben keletkező vegyületek révén fokozzák a forraszanyag nedvesítő képességét. A gyakorlatban jól bevált anyag a a fenyő gyanta és a cink-klorid + ammónium-klorid elegye. Ez utóbbi elég korrozív anyag, így a forrasztás végén gondosan meg kell tőle tisztítani a felületet. A mai forrasztástechnikában persze már létezik olyan termék, ami nem korrozív és így a mosástól is el lehet tekinteni, de ezek nem olcsók.
Forrasztópáka:
A forraszanyag megolvasztásához ipari méretekben kádakat (hullámforrasztás) használnak, kézi forrasztáshoz pedig ún. forrasztópákát. A forrasztópáka tulajdonképpen egy nyéllel ellátott fűthető fémdarab, melynek hegy kialakítása igen változatos lehet az alkalmazási területnek megfelelően. A hevítést legtöbb esetben a elektromos áram végzi a pákanyakban elhelyezett fűtőszálon keresztül, de speciális esetben (pl. mobil alkalmazásokban) találkozni pl. öngyújtó gázzal működő kivitellel is. A pákákat a helyes és tartós működés érdekében termosztálni kell, vagyis biztosítani kell a viszonylag állandó üzemi hőfokot. Ezt a fűtőszál szabályozott, be-/kikapcsolásával lehet elérni. Erre a szabályzásra számos módszert fejlesztettek már ki:
-
a páka nyelében elhelyezett, különböző hőfokokra méretetzett, cserélhető termosztát gombák,
-
a pákahegy végén különböző mágnes pogácsák alkalmazása. Ennél a megoldásnál a „hideg” pákahegyet a mágnes odafogja a fütőszálhoz bekapcsolva azt, majd a felmelegedés egy (beállított) hőfokán a mágnes drasztikusan veszít a megnesességéből, így egy kis rugó el tudja távolítani a fűtőszáltól. A folyamat reverzibilis, vagyis visszahűlve a mágnes ismét le tudja győzni a rugó erejét, és a fűtés újra indul. Ilyen elven működik az elektronikában fogalomként ismert Weller-páka. A pákahegyek mágnesén lévő szám utal a hőfokra.
-
A legkomolyabb és legnagyobb rugalmasságot biztosító megoldás, amikor a páka fűtését vezérlő elektronika a páka tartóval kombinálva egy külön egységben kap helyet, melyen a kívánt hőmérsékletet széles tartományban be lehet állítani. Ezt a szakzsargon pákaállomás-nak hívja. Ezen az egységen a hőmérséklet kontrollálásához helyet kaphat egy LED-sor vagy akár digitális kijelző is.
A pákahegyek (melyek változatos alakúak) rendszerint könnyedén cserélhetők a pákában.
A forrasztó munkaállomások elengedhetetlen kelléke a pákaszivacs is, melyet benedvesítve alkalmaznak. Célja, hogy a pákahegyről a kiégett folyasztószert és maradék ónt le lehessen törölni. Ez a szivacs egy speciális anyag, senki ne próbáljon helyette mosogató szivacsot használni, mert 300..400°C-ot is ki kell bírnia! A könnyebb salakanyag leválasztás érdekében a szivacson lehetnek lyukak is. A nedves szivacson a pákahegyről lesodort forraszanyag egy pillanat alatt megdermed és apró – gyöngy szerű – göbökben gyűlik a szivacs tálcán. Az áramköri panelek gyártása és javítása közben keletkezhetnek olyan ónpacák, melyeket el kell távolítani. Erre a célra ónszívó szalagot vagy ónszippantót lehet alkalmazni. Az ónszívó szalag igen erősen vonzza magához a megolvadt forraszanyagot, így gyakorlatilag eltávolítja azt eredeti helyéről. Kis tekercsben forgalmazzák. Az ónszippantó egy mechanikus szerkezet, mely egy erős rugóval megfeszített dugattyú. A tubus elszűkülő teflon csúcsban végződik. használat közben a megfeszített rugót hirtelen elengedve a dugattyú vákuumot képez és így a megolvadt forraszanyagot egyszerűen beszippantja.
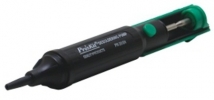
Kézi szerelés (THT) / gépi szerelés (SMT):
Az ipari méretekben történő áramkör gyártás nem csak a NYÁK lemezek készítését, de a panelek beültetését is gépesítette. Ezt a műveletet SMT-nek nevezzük. A hagyományos huzal lábas (THT) alkatrészek helyett ezért megjelentek a panel felületére ültethető, ún. SMD alkatrészek. Ezeket egy X-Y-Z vezérlésű robotkar vákuummal felszippantja precízen a helyére teszi. Az alkatrészek forrasztását sem pákával végzik, hanem ún. forraszpasztával kemencében hevítve. A pasztát a panel montírokra a szitanyomáshoz hasonló módszerrel viszik fel. A NYÁK tervezéssel együtt készül egy olyan dokumentáció is, ami foltokban megadja, hogy hova kerülnek majd az SMD alkatrész lábak, így erről a képről készíthető egy (általában) fém lemezből kivágott maszknak nevezett sablon, mely lyokas ott ahol a panelt pasztázni kell. A maszkot egy asztalon a panelre fektetik és egy lemúzó lemezzel a pasztát végig kenik a felületen. A lukakon keresztül a paszta a NYÁK-ra tapad. Amikor az ültető gép az alkatrészt a panelre helyezi, annak lábai besüppednek a paszta rétegbe és megtapadnak azon. A gyártás következő fázisában az így előkészített montírt a kemence hosszán keresztül vezető futószalagjára helyezik. A kemence több hőmérsékleti zónából áll, melyeken a panelek áthaladva egy előre beállított idő-hőfok függvény szerint történik a forrasztás. Ennek során a paszta megolvad, a benne lévő folyasztószernek köszönhetően körbefutja az alkatrés lábat, majd a kemencéből kifelé jövet megdermed.
A méretük vagy egyéb paraméterük miatt géppel nem beültethető alkatrészeket továbbra is kézzel (THT) forrasztják a panelba. Ez történhet pákával vagy egy szintén futószalagosítható hullámforrasztásnak nevezett eljárással, amikor is a panel (a kézzel csak behelyezett alkatrészekkel) egy megolvasztott ón szökőkút felett elhaladva kapja meg a forrasztást.
Ennyi elmélet után nézzük, hogyan is forraszzunk:
-
Fontos feltétel, hogy a forrasztandó alkatrészek tiszták legyenek. Ha oxidos a láb, óvatos kapargatással kell azt eltávolítani. Ha az alkatrészek (pl. ellenállások, diódák) láb vége a hevederből kihúzva ragasztós marad, akkor azt inkább vágjuk le, mert ezt megforrasztva nemcsak büdös, de elszennyezi a pákahegyet is.
-
A forrasztandó alkatrészeket tartsuk a lehető legközelebb egymáshoz. Ne feledjük, a forraszanyag csak összefogja az alkatrészeket, nem pedig áthidalja a nagy réseket!
-
Az általános célú forrasztáshoz a legmegfelelőbb hőmérsékleti tartomány a kb. 360°C. Ha kényszerűségből ennél hidegebb pákánk van, akkor félő, hogy ún. hidegforrasztás keletkezik, amikor is a forraszanyag nem tud elég erős adhéziós kötést kialakítani az alakatrészláb felületén. Ez idővel (pláne ha még mozog vagy rázkódik is) meglazulhat és kontakthibát okoz. Nem jó a túl meleg páka sem, mert a magas hő jobban igénybe veszi (vagy akár tönkre is teheti) az alakatrészeket. Ilyen esetben iparkodni kell a forrasztással, hogy 1-2 másodpercnél tovább ne tartson! Mivel az ólommentes forraszanyagok nagyobb hőfokot igényelnek, ilyen esetben a gyakorlott, gyors mozdulatokra fokozottan szükség van.
-
Ha a forrasztás során az a tapasztalat, hogy a forraszanyag nem futja be kellően a felületet, plusz folyasztószer alkalmazása javasolt. Ez különböző összetételben beszerezhető tégely vagy tubus formájában. A tégelybe a meleg pákahegyet „mártogatjuk”, a gél állapotút viszont pl. fecskendővel, ecsettel lehet a munkaterületre kenni.
-
A forrasztás folyamán – még ha bele is lendülünk – ne feledjük gyakran tisztítani a pákahegyet; amikor pedig rövidebb-hosszabb időre visszatesszük a pákát a tartóra, előtte mindig töröljük le a hegyet, uganis a hegyre ráégő folyasztószer maradékok korrodálhatják a hegyet.
-
A forrasztás után a felületet meg kell tisztítani a folyasztószer maradékoktól, mert a korrózió idővel „megeszi” a forrasztási pontokat és (még a lakkréteg alá is bekúszva) a huzalozás réz anyagát.
|